
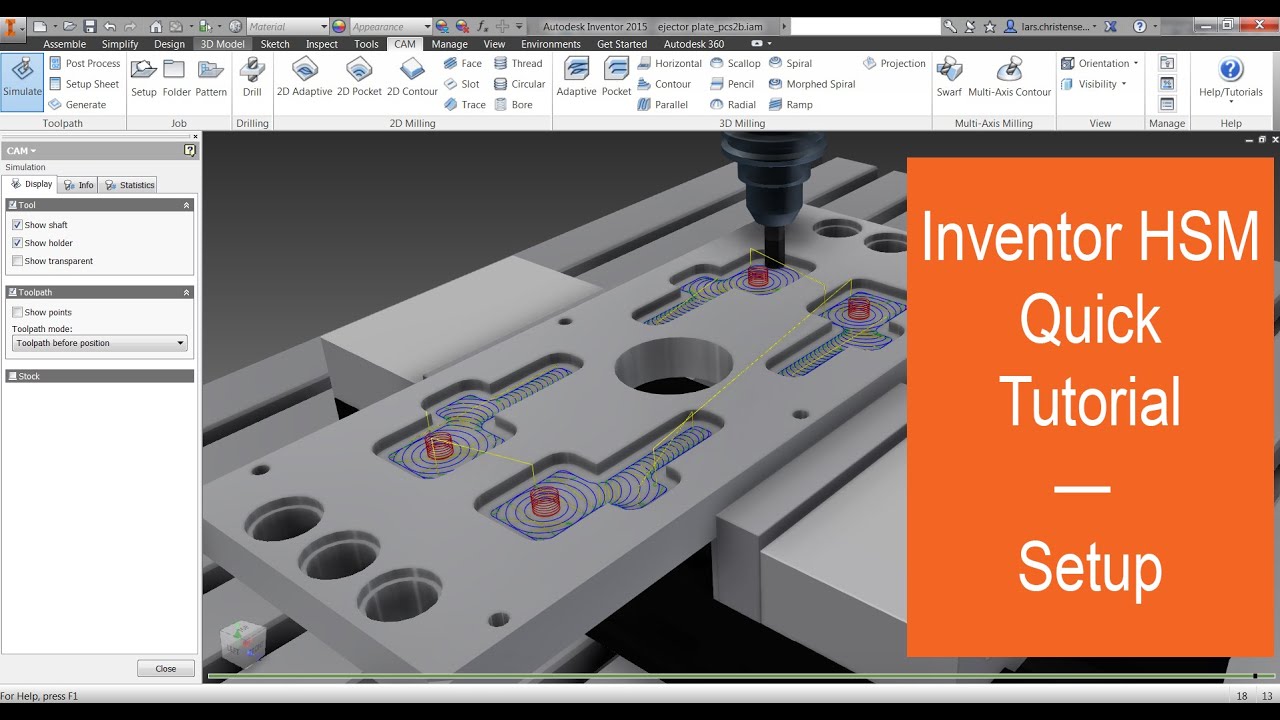
On multiple occasions we discover a design issue at 5pm and I am fitting a new version of the part at 10am the next morning, this makes a big difference in R&D and my clients appreciate that.” Overall, it has been a better value for my clients for me to make parts than conventional prototyping services and the parts are often better. I have added a 5th Axis dovetail fixture and by keeping tool lists and stock together I can make replacement parts very quickly. If I need to run a small batch I can, especially if the tools are pre-measured.
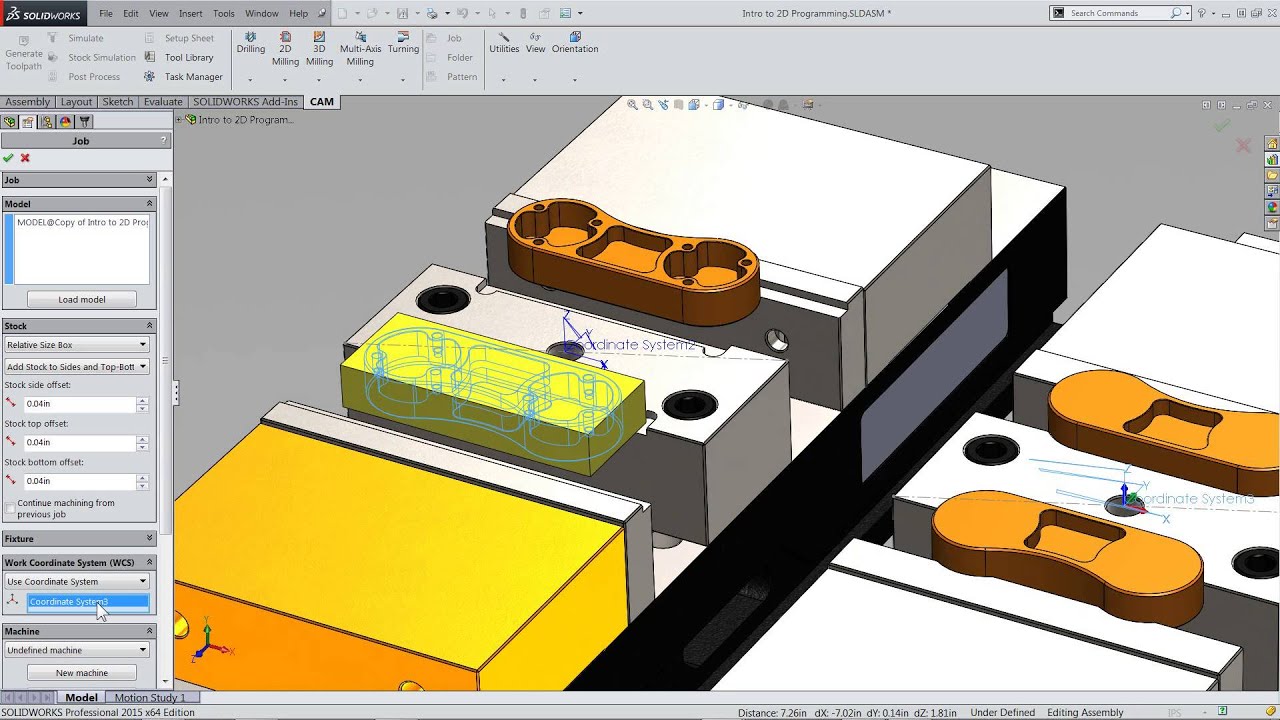
“The key to the work I have done with the Pocket NC has been rapid turn-around, I can make one-off complex parts without tooling and without soft jaws in one go. To learn the Pocket NC he went through the basic first part tutorial and utilized Titans of CNC 5-axis tutorials to get going. HSMWorks is supported by the same post as Fusion 360, since both are Autodesk products. To program the Pocket NC he uses HSMWorks since it offers a plugin with Solidworks.
#Hsmworks manual manual#
Graham has a background in manual mills and lathes, and additionally has retrofitted and scratch built several CNC machines. The 5-axis positioning means one set-up is enough for most of the parts I make and this saves a huge amount of time and reduces the margin for error a great deal.” Overall, it is closer in speed to a machine with ATC than a manual machine, add collars to the tools and pre-measure and you can be faster than some ATC machines with practise! Built in tool measurement is also excellent.
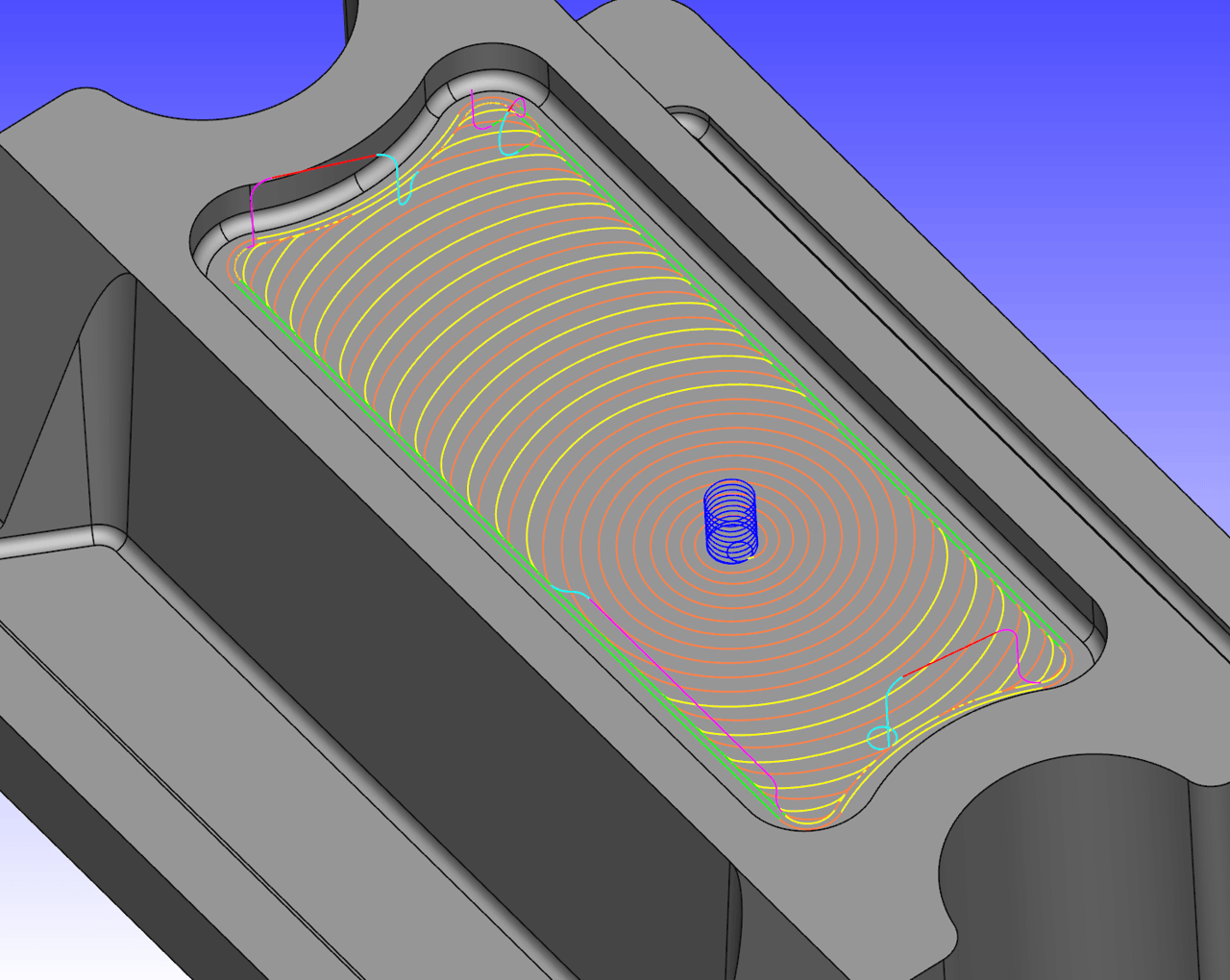
I love the lever operated tool change as well, compared to a collet and nut it is amazing. A high-speed spindle is essential for small cutters and that is what I use most of the time. “The main things that drew me to the V2-50 machine were its spindle and the ability to do positional 5-axis work. For one-offs this was fine, but they might take a whole afternoon for a single small part.” On Choosing and Learning the Pocket NC Then typically there would be some additional cross-holes to drill which would tend to be done on a manual mill. Initially this was done on a self-built CNC machine based on precision stages, tool changes were all manual. Often dowels would be added to help alignment and take some cutting forces. “My workflow was generally to do a first op from stock, then machine a fixture to accept this half finished part in the tooling board or aluminium and glue the part in place before the second op. Prior to acquiring a Pocket NC Esotechnic’s workflow was as follows:
